Triebwerkstests in Peebles
Neben der Funktion der Antriebe muss GE auch ihre Robustheit nachweisen. Für den Bläser bedeutet das vor allem die Widerstandsfähigkeit bei Vogelschlag. Mit einer Aufschlaggeschwindigkeit von rund 330 km/h werden beim entsprechenden Experiment die Start- und die Landephase eines Verkehrsflugzeugs simuliert. Die Palette der Vögel reicht von vier rund ein Kilogramm schweren Tieren auf einmal bis hin zu einem einzelnen, 3,6 Kilogramm wiegenden Vogel. Vorher werden sie geröntgt, um sicherzustellen, dass keine Bleikugeln oder ähnliches enthalten sind, und anschließend tiefgefroren. Eine pneumatische Kanone katapultiert sie dann ins Triebwerk. Noch spektakulärer geht es beim „Blade-out“-Versuch zu, der bei jedem neuen Muster mit Spannung erwartet wird. Hier trennt eine Sprengladung eine Bläserschaufel ab, die dann das Gehäuse nicht durchschlagen darf.

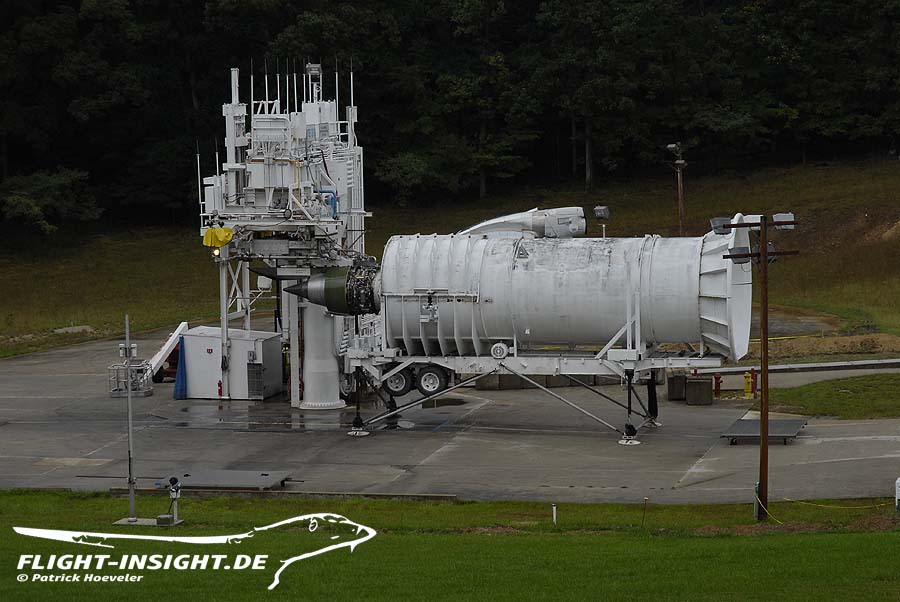
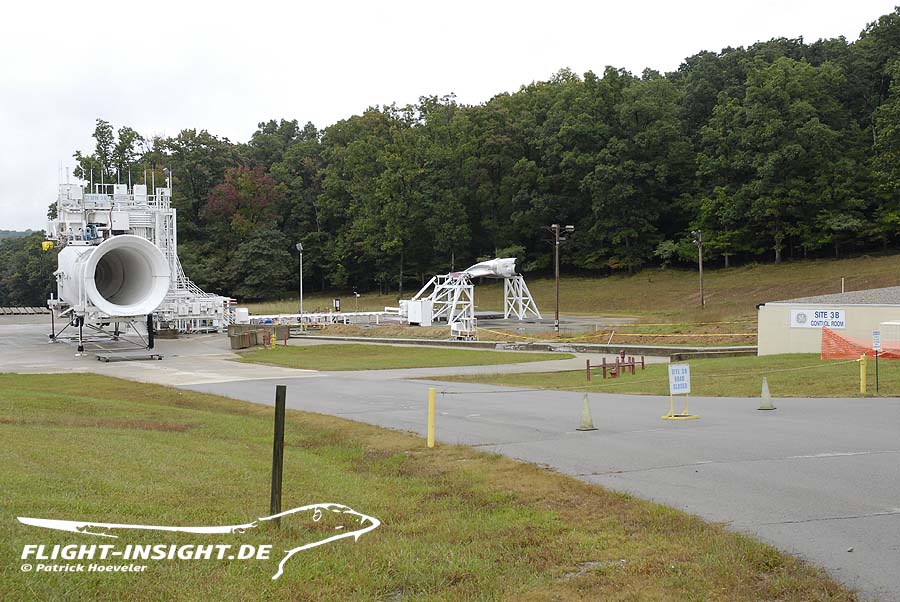
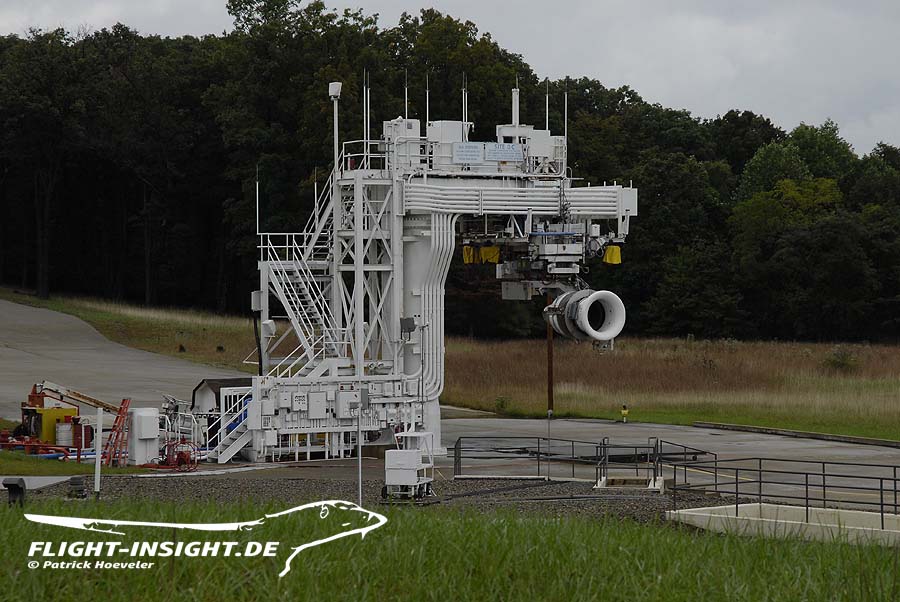
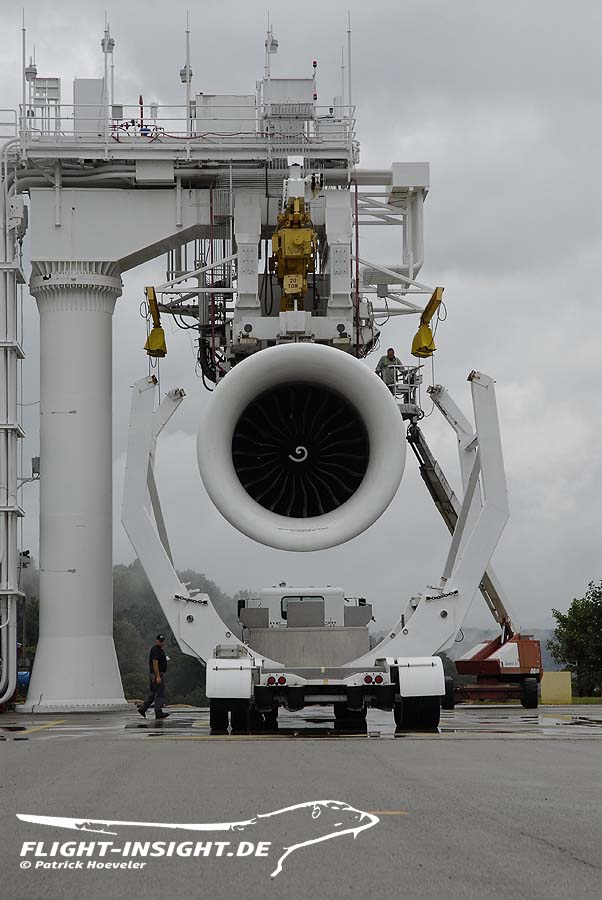
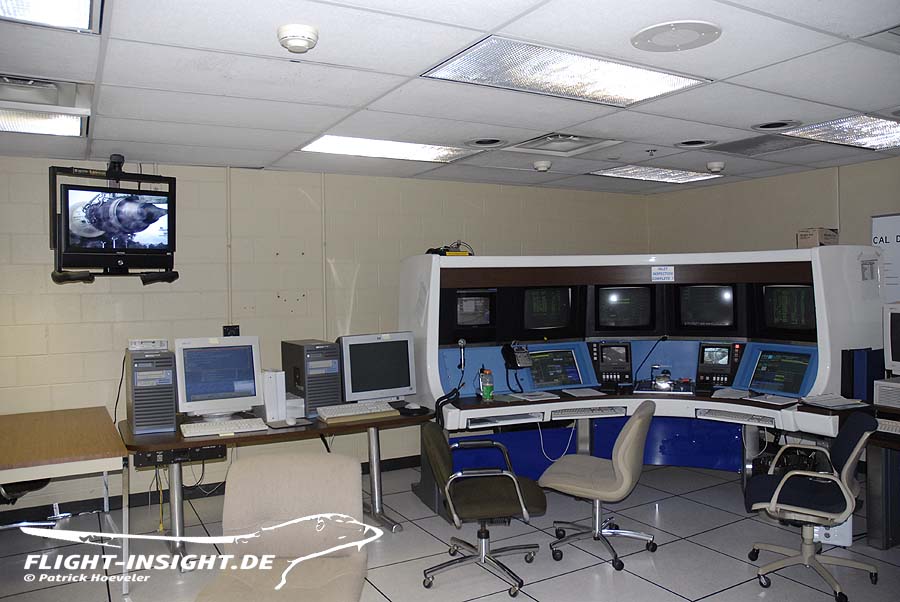
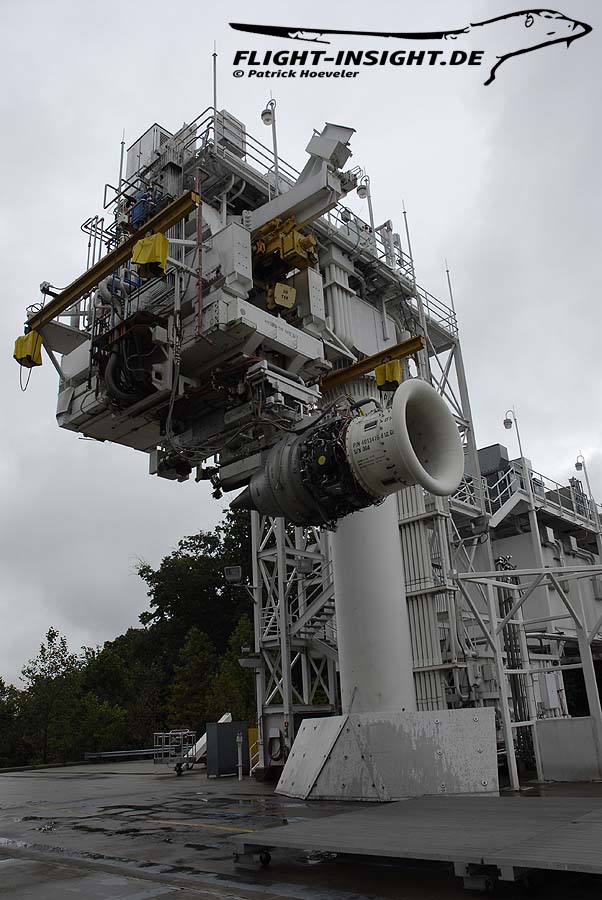
The engines of today’s commercial aircraft are subject to the strictest safety regulations. They must also guarantee safe operation despite ice and hail ingestions, or bird strikes. That is why engine manufacturers simulate all conceivable situations on their test stands for the approval of their products. Even the units from series production are put through their paces before they make their way to the customer. GE Aviation’s outdoor facility in Peebles, located about 100 kilometres from Cincinnati in Ohio, was the largest and most versatile facility for testing aircraft engines in the world when it was visited in 2006. At that time, more than 1000 engines were running here at the Peebles Test Organisation (PTO) annually.
A total of eight test stands are used for this purpose, six of them in the open air. The company had already bought the site from the US government in 1957 for testing rocket engines. In addition to secrecy, noise also played a role in the choice of the secluded area, which at more than 27 square kilometres is only slightly smaller than the Frisian island of Borkum, for example.
One of the largest test stands is number 3E; it can handle engines with a power of up to 667 kilonewtons. The centre line of the unit must be at least six metres above the ground to ensure a good air supply without disturbances. A smaller version still manages 338 kilonewtons at a distance of five metres. Two winches lift the test specimen – such as a GE90 with a dry mass of more than eight tonnes – from the trailer of a truck so that the workers can couple the giant engine to the mounting frame via an adapter. Four hydraulically actuated bolts, each with a diameter of ten centimetres, ensure a secure hold. A standardised adapter connects all fuel and other lines. Thus, the installation takes just half an hour.
For the approval of a new model by the US Federal Aviation Administration (FAA), GE, like all manufacturers, must prove that the engines will function safely even under adverse weather conditions. For this reason, the specialists in Peebles go to great lengths to simulate a wide variety of situations. For example, a wind turbine mounted on rails, which can be rotated as needed, can generate wind speeds of up to 160 km/h with numerous small propellers. It is mostly used for crosswind tests.
If performance measurements are required, the so-called “Turbulence Control Structure” (TCS) is used. It resembles a gigantic golf ball and is positioned directly in front of the air intake. It consists of a perforated honeycomb structure and is therefore 60 per cent permeable. The device calms the incoming air flow and thus enables more accurate measurements.
Contact with water, ice or hail is also a real challenge. A powerful battery of spray cannons blows water into the engine to recreate a flight through a heavy rainstorm, up to 4500 litres per minute. For ice and hail tests, lorries have to bring in tonnes of ice from the nearest village, which is then crushed and measured into specific sizes by a special machine at Peebles. The pieces of ice are then shot into the unit for 45 to 60 seconds from 19 cannons for large models or seven for smaller ones.
In addition to the function of the drives, GE also has to prove their robustness. For the fan, this means above all resistance to bird strikes. With an impact speed of around 330 km/h, the take-off and landing phases of a commercial aircraft are simulated in the corresponding test. The birds range from four birds weighing about one kilogram at a time to a single bird weighing 3.6 kilograms. Beforehand, they are x-rayed to ensure that there are no lead bullets or similar, and then deep-frozen. A pneumatic cannon then catapults them into the engine. Even more spectacular is the “blade-out” test, which is eagerly awaited with every new design. Here, an explosive charge separates a fan blade, which is then not allowed to penetrate the casing.